前回「なぜなぜ5回」の「5回」にとらわれるなという話をした。では一体どこまで繰り返せばよいか。簡単にいえば、「狙いどころまで『なぜ』を繰り返していく」べきである。「狙いどころ」としては、「真因(または根本原因)を探る」などが考えられる。問題が発生したときに、上司から「『なぜ』を繰り返して真因を探れ」と命令されたことがある方も少なくないだろう。
しかし、狙いどころを「真因を導き出すこと」と安易に考えて分析を進めてはいけない。それを真に受けて「なぜ」を繰り返していくと、やれ「疲れていた」だの、「商品の種類が多い」「作業が増えた」など、対策から遠ざかる「なぜ」が出てきてしまったり、「○×部品が壊れた」が真因にされてしまい、「○×部品を交換する」といった真の再発防止にならない処置で対策が終わってしまうことになりかねない。
的外れな「なぜ」や、中途半端なところで「なぜ」の繰り返しを止めないためには、「分析の狙い(落としどころ)は、再発防止策を導くことである」としておく必要がある。
気づける体制のない“再発防止策”では再発必至
ただし、「再発防止策とは何か」を分かっていないと、また同じことになる。そこで、私は1997年に「再発防止策」の定義を以下のように定めた。
(2)「発生したとしても、許容できる範囲内で『気づきやすく』『気づける』体制にす る、気づいた後に的確な処置ができるようにする」
「発生しないようにする」策は複数あり得る。例えば「ボールペンをカバンに入れ忘れる」ことに対して、「ボールペンに紐をつけてカバンに結びつけておく」といった発生を完全に防ぐ策もあるし「カバンごとにボールペンを入れておく」といった、発生しにくくする対策も含む。
一方、「発生したとしても、許容できる範囲内で『気づきやすく』『気づける』体制にする、気づいた後に的確な処置ができるようにする」とは、「カバンの外にボールペンを引っ掛けるところを作り、外観でボールペンがないことにすぐ気がつくようにする」こと、同時に「すぐ補充できるよう予備を1本つねに購入しておく」といった対策のことである。
ここで、再発防止策には「レベル」があることを忘れてはいけない。レベルとは、現場・職場・ラインだけで食い止められるのか、部単位で、あるいは別の部署や会社全体で食い止める対策が必要かどうかということである。
例えば、導き出した「なぜ?」が、別の部署やほかの会社(材料、部品、設備、物流、サービス)などが絡む話だとしよう。すると「この『なぜ』の続きは、そちらの部署でやってもらう」と分析のバトンタッチをして、自部署だけでなく、包括的に対策が実施されるように仕向けなければならない。すなわち統括者や管理者は、どのレベルで発生トラブルを食い止めるべきかをしっかり考えたうえでなぜなぜ分析を指導しなければならない。
このことを図で表すと以下のようになる。
もちろん、初めは当事者たちが分析し、自分たちで実施しなければならない対策を当事者自らが導くことから始める。最初の分析には、第3者(関連のあるスタッフなど)を加えることをお勧めしたい。誰しも偏った考え方やとらえ方はしがちであり、もし考え方・捉え方で抜けている点があったとき、当事者だけでは気づけないケースが多いからだ。
次回は、具体的に「リスク管理体制でしばしば見受けられる不備・誤解」について提言したい。
(次回に続く)
マネジメント・ダイナミクス 社長
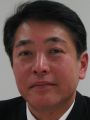
マネジメント・ダイナミクスのホームページ:http://management-dynamics.co.jp/