広島市に本社を置く自動車用機械部品のプレス製造会社、住野工業の住野重樹社長は、2003年12月期の決算を締め終えたとき、ここ10年にない成果に目を細めた。主事業である自動車用部品の量産事業が過去10年で最高額の利益を上げたからだ。
同社の2003年度の売上高61億円のうち、金型製造などの売り上げを除いた「量産事業」の売上高は対前年度比15.6%増の52億円。同事業の営業利益は対前年度比4倍の約4億円に急伸した。営業利益率は8%弱にもなる勘定だ。2002年度は量産事業の営業利益率は2%程度にすぎなかった。金型関連の利益が中心だったのだ。
2004年度は「量産事業は売り上げが2割増の62億円、営業利益率は8%を維持する」(住野社長)考えだ。全社では66億円、営業利益は5億円を見込む。
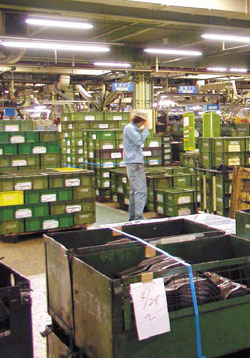
生産管理にTOCを導入
同社が2003年度に利益を大きく伸ばしたのは、同年春から生産管理の変革のためTOC(制約条件の理論)に取り組んだ成果だ。TOCとは、問題点(問題工程)を部分的に解決するのではなく、全体最適の視点からその問題(ボトルネック)を解決していくという手法である。
営業と購買の現場責任者である、営業購買部営業購買Grマネージャーの中川良司氏が2002年秋にTOCの解説書である「ザ・ゴール――企業の究極の目的とは何か(ダイヤモンド社刊)」を読んだことがきっかけで、導入は始まった。
「当社の工員は半数が人材派遣。トヨタ流ジャスト・イン・タイム(JIT)方式のように全員参加型の改善を徹底するには、人の入れ替わりが激しすぎる。TOCのように重点となるプロセスを管理する考え方のほうが当社に向いていると思った」(中川マネージャー)
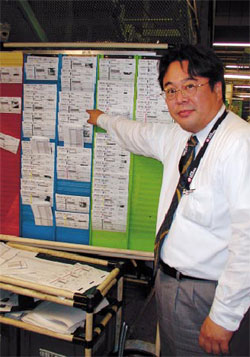
中川氏は、TOC関連のツールやコンサルタントを調べ、「経営陣や生産現場のリーダーなどキーパーソンを集めてTOCを理解するワークショップを開きたい」と住野社長に直訴した。しかし、コンサルティング会社の見積もりは200万円と気軽に出せる金額ではない。住野社長はこう話す。
「中川マネージャーの勧めで本を読んだときは、ロジカルで整然としたいかにもアメリカ的な方法で、うまくいくかもしれないと思った。思い切って、まず経理や総務、生産管理、プレスなどのリーダーを交えた講習会を開いた」
生産管理に危機感
中川マネージャーの上司で、やはりワークショップに参加した佐藤丈夫専務は、「すぐに効果を確信できたわけではなかった。それでも、何かを変えたいという気持ちが強かったので、最終的にTOC導入に賛成した」と当時を振り返る。
佐藤専務が言うように、住野工業は当時、非効率な生産状況だと認識しながら、解決策がなかなか見つからずにいた。
同社の製造工程は、2つの工場をまたいでいる。プレス工程は、本社から北に車で高速道路で1時間ほど走ったところにある広島県高宮町の高宮工場で行い、その下流工程の塗装や研磨などを広島市内の本社工場が行う。なぜプレス工程だけが隔離されているのかといえば、本社周囲への騒音公害を考慮してのものだという。
自動車用部品製造の生産管理は、何より納期順守が至上命題だ。ところが、同社の製造ラインは常に900品種が流れており、散発的に製造する部品も含めると年間で2500品種以上を手掛けるだけに部品製造状況の把握は容易ではない。
本社工場側で1つでも納期に間に合いそうにない部品が見つかると、現場は慌てて、高宮工場に電話をかける。急いで段取り換えをして、製造するように依頼をするのが当たり前になっていた。「本社工場の班長は、1日中、高宮工場に電話して、督促をかけているような状況だった」(中川マネージャー)
こうした危機感のもとに、昨年3月、正式にTOC導入プロジェクトを開始した。コンサルティング契約を結んだ日本総合研究所(東京・千代田)は、まず同社の工場を流れる部品をルート別に20数種類のグループに分けた。例えば「プレス→研磨→組み立て→塗装」あるいは「プレス→シム加工(精密加工)」などだ。そしてそれぞれの制約工程を特定した。
その結果、高宮工場内ではあるプレス工程が、そして本社工場内ではルート別に塗装工程、シム加工と呼ばれる精密加工工程、バレル研磨工程の3つのポイントが、「制約工程」として設定された。
このように制約工程を重点管理するのがTOCの生産管理手法であるDBR(ドラム・バッファー・ロープ)の骨子だ。
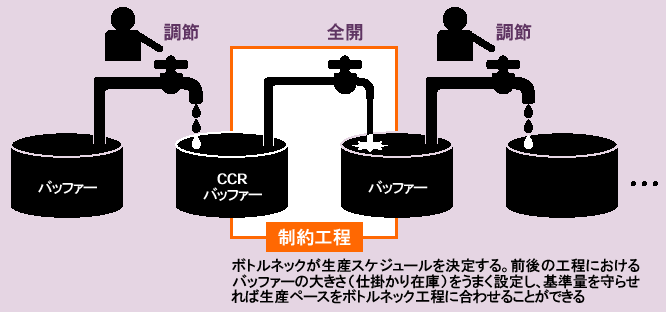
制約工程の上流の工程は、制約工程の直前に置く「バッファー」と呼ばれる仕掛かり在庫置き場の状況を見て生産ペースを調節する。バッファーに置く仕掛かり在庫の基準量を事前に定めておき、あふれそうになれば、上流の工程は生産スピードを落とし、少なくなりすぎれば、生産ペースを上げる。
日本総合研究所によれば、「基準量は、資材投入工程から制約工程までの間の処理時間と、同区間で過去に起きた最長トラブル対処時間の合計をベースに決めるのが原則」という。
中川マネージャーはその後、さらに部品のグループ分けを細かくし、その生産計画を30数種のグループごとに分けてIT(情報技術)ツールで管理している。同社では、早朝にマツダなど取引先から3日先の確定注文情報がオンラインで流れてくると、まず従来からあるMRP(資材所要量計画)ツールで資材投入量を決める。このデータをスケジューラーという計画ツールに移して、ボトルネック工程がフルに稼働できるよう考慮した投入順序などを決める。
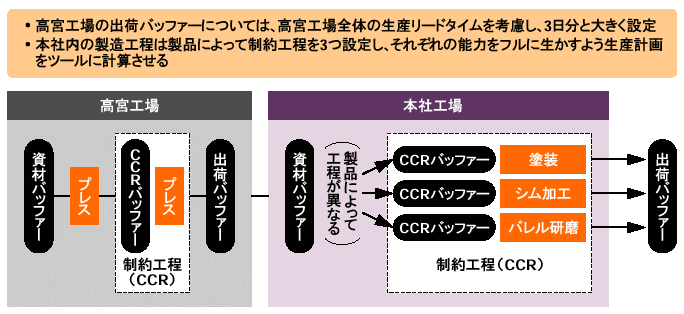
このスケジューラーは、ジェィティ エンジニアリング(東京・港)の「Joy Scheduler」というツールに独自に機能改良を加えて導入した。スケジューラーと併せて、工場内にバーコード管理システムも導入した。製造部品が主要工程を通過するときバーコードで読み取り、流れをスケジューラー上で一元的に把握できるようにした。2003年のIT関連の投資は計3000万円程度になったという。
増産余力などが見える
スケジューラーの開発を終え、まず本社の工場では昨年9月にDBRを本格実施し始めた。すると、管理すべきポイントが明確になり、製造現場が勝手な見込みで生産ペースを判断しなくて済むようになった。「制約工程の状況さえ見ていれば、在庫やどの程度増産の余力があるかなど大体わかるようになったから、納期回答もしやすくなった。安心してマツダ以外の受注も取れるようになって売り上げが増えた」(中川マネージャー)
高宮工場の生産計画のやり方を抜本的に変えた結果、時間外労働を削減できたにもかかわらず、本社工場への納期順守率が飛躍的に向上した。
もともと、本社と高宮工場のコミュニケーションには問題があった。同社ではマツダから月次で内示を受け取った後に、日々の注文量が確定するのは納品3日前だ。しかし、高宮工場と本社工場をまたぐ工程は標準で11日間を要するために、実際は見込み生産を行い、確定情報を受け取ってから慌てて、見込みとの差分を埋めるために督促をかけることが頻発していた。日々の確定情報は、月次平均量に比べて最大で20%程度上下するからだ。
これが、予定外の緊急な段取り換えを頻発させた。特に高宮工場ではプレス工程の段取り換えは時間がかかるため、稼働率が大きく下がる。
しかも、本社工場の現場が、生産管理担当者に記録を残さず、めいめいに電話で高宮工場に緊急生産を要請した結果、翌日には新たにMRPツールから増産指示が二重に飛んでしまったりする。これは今度は作り過ぎを招く。高宮工場では「不足品がある一方で、在庫もどんどん膨れ上がるという状態になってしまった」(佐藤専務)
そこで高宮工場は、本社への出荷口に設けたバッファーを中心に生産ペースを調節することにした。このバッファーに3日分の在庫を置くこととして、このバッファーの量が一定になるよう日々の生産計画を立てる。当然、出荷と生産は1日ごとに見ればかい離が生じるが、それは3日分の在庫によって埋める。
生産効率化のために、3日分の在庫置き場を設ける――ちょっと見ると矛盾した発想だが、「昨年10月から高宮工場の一部のラインで実施したところ、未納数量が10分の1以下に減った。しかも同程度の生産量であれば、時間外労働も半分以下で済むようになり、仕掛かり在庫も減った。それまでの混乱がウソのように安定している」(中川マネージャー)。最悪の時には丸1日分を上回る遅延が発生していたが、一気に悪循環が解消された。やみくもな段取り換えや、本社工場からの督促が消滅したための効果だ。
今年度は、高宮工場内でのDBRも実施するほか、材料メーカーからの調達にもTOCを応用する予定だ。
現場改善も大事だが、仕組みを変える効果は大きいもともと明治時代には足袋(たび)の留め具であるコハゼの量産を手掛けていた。最盛期には女性工員を200人抱え、全国の需要の4割程度を生産していた。真鍮(しんちゅう)で培った加工技術を生かして、1960年からはマツダの部品製造を始めた。 バブル崩壊直前の91年は売上高が101億円だった。営業利益率では昨年が最高だったが、利益の絶対額はまだ当時のほうが上回っている。 当面はまず売上高を連結で最低100億円に戻すことが課題だ。当社は最終赤字を一度も出していないし、一昨年、昨年とマツダから成績優秀賞をいただき、コスト削減力や品質力には誇りを持っている。だが、生き残るにはやはり規模も重要なファクターだ。今後は、アルミやマグネシウム合金の塑性加工で顧客や事業拡大の道を探る。 一方で 生産の効率化には、現場の改善活動ももちろん重要だが、仕組みを適切に変えていくことの効果の大きさを、TOCの導入で痛感した。中川マネージャーのほかに、高宮工場でもTOCの推進者を育てているところだ。(談) |