AI(人工知能)技術が、ものづくりの生産現場を劇的に変えようとしている。部品の仕様や生産ラインを変更してもスピーディーに対応できるよう、部品の組み立てや各種検査に使う画像認識システムのプログラムを自動的に生成・修正することが可能になってきたからだ。この技術に5年にわたり取り組んできた富士通研究所は、グループ会社での実践を通じて、電子部品の生産性向上やQCD(品質・コスト・納期)の改善という目に見える成果を上げてきた。
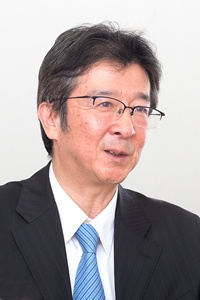
ものづくり技術研究所
特任研究員
肥塚 哲男氏
電子機器の生産ラインでは以前から、画像認識システムが導入されてきた。部品の実装装置、はんだ検査装置、部品組み立て装置、製品外観検査装置など、完成品に至るまでのプロセスで、カメラを用いた自動組み立てや検査が行われてきたのである。
例えば外観検査であれば、対象物にいろいろなパターンの照明を当て、備え付けのカメラで画像を撮影し、画像認識システムによって欠陥を検出する。今まで人が目視で発見していた傷や汚れや異物の付着など微細な欠陥を一括して検査できるので、QCD(品質・コスト・納期)の大きな改善が期待できるからだ。
しかし、製造業では、部品の仕様変更や生産ラインの立ち上げ・変更といったニーズに、より柔軟に、かつスピーディーに対応することが求められるようになってきており、その際に画像認識システムがボトルネックになるケースが増えてきている。生産ラインが変更されると、画像認識システムのプログラムの調整や再構築が必要になるからだ。
富士通研究所で画像認識システムの開発に長年取り組んできた富士通研究所 ものづくり技術研究所の肥塚哲男特任研究員は「画像認識システムのプログラム開発は時間がかかるうえに、生産ラインごとに具体的な実装方法を検討しなければなりません。生産ラインの明るさや照明の角度、カメラの位置などによって、撮影される画像が微妙に変わってくるからです。生産ラインの立ち上げ時には、毎週のように現場に通ってプログラムを調整します」とその難しさを説明する。
継続的なメンテナンスも必要になる。生産ラインが変更されたり、部品の仕様が変更されたりすることで、撮影した画像が正確に認識できないケースが生じてしまうからだ。「変更のたびに、開発者が現場に行ってプログラムを修正しなければなりません。これまでは現場に行って状況を把握し、画像を見ながらプログラムを書き換え、きちんと動くことを見届けるのに1週間くらいかかっていました」と肥塚氏。その分、生産ラインの立ち上げ時期も遅れることが課題になっていた。