制約工程を起点に投入量を見直す
まず2006年1月から製造部門でDBRを実践し、2006年9月に設計部門でCCPMを導入した。2009年3月現在で、受注から試作品の納品までのリードタイムが従来の2~3カ月から2週間へと最大83%短縮した。また量産時の受注から納品までのリードタイムや、工場内の仕掛かり在庫は半減した。
TOCのDBRとはどのようなものか。水の流れで例えると分かりやすい。蛇口の大きい水道管と蛇口の小さい水道管が垂直に連なり、中間に水をためるたらい(バッファー)がある。蛇口の水量が少ない中間の水道管に全体のペースを合わせれば、各工程の仕掛かり在庫を減らせる。ペースを合わせるには、前工程がバッファーを常に見て生産すればよい。また、水の量が少ない水道管の稼働率を重点的に高める投入スケジュールを組み全体最適を図る。
そこでDBRでは5つの実行ステップで物の流れを変える。(1)生産能力向上のボトルネックとなっている制約工程を見つけ出す、(2)見つけ出した制約工程の稼働率を最大限に伸ばす、(3)作り過ぎの無駄を防ぐためほかの工程を制約工程の生産能力に合わせる、(4)制約工程を強化する、(5)揺り戻しに気をつけつつ(1)に戻る──だ。
まず3カ月かけて(1)の「制約工程を見つけ出す」に取り組んだ。社内外で1つずつ制約工程があった。そこでまずは特定商品に対象を絞って、グループ会社の1社とともに製造工程の管理を見直した。見直しのポイントは社内の制約工程である焼成工程関連では主に3つ、社外の制約工程である加工工程関連では主に2つあった。
社内の焼成工程関連での改善の1つ目は、焼成工程に1回当たり投入する量を従来の30~40%に減らしたこと。1回当たりの投入量を減らしたほうが、前工程から製品が届き次第、生産順序を変えることなくすぐに焼成に取りかかれるからだ。
2つ目は、10以上ある炉の稼働開始時刻を鉄道の時刻のように決めたこと。これも焼成工程の担当者が恣意的に生産順序を変えずに済むようにするためだ。焼成工程は、釜に工具を入れて焼き固めるものだが、製品や材質の特性によって細かい温度調整が必要な多品種少量型の生産工程だ。しかも「現場担当者の主な評価項目は、その工程での1個当たりの焼成コストを下げることだった」(中村洋製造部長)。従来は、前工程から流れてくる仕掛かり品が釜の最大容量に達した品番から焼成をしていた。
3つ目は、炉の能力の向上だ。炉自体を改良して焼成時間を20%以上短縮した。また、焼成できる炉が少なかったセラミック材料の工具に対応する炉を増やした。
前工程のペースをボトルネックと同期
社内の制約工程である焼成工程に、その前の工程の物の流れのペースを合わせる取り組みも実施した。焼成工程とその直前であるプレス工程は、投入スケジュールなどを毎朝確認する「もしもしミーティング」を開き、同期を取った。そして、前工程のプレス工程も、焼成と同期を取るために、現場判断で投入順を変えることのないよう改めた。
プレス工程と、その直前の工程である乾燥造粒の工程との間の仕掛かり在庫は、「焼成工程の生産能力の3倍を超えない」という管理ルールを作った。これは台車の搭載量を標準化して、台車の量を目安に現場で管理している。
一方、社外の制約工程である加工工程に関する改善の取り組みの1つ目は、まず仕掛かり在庫の見える化だった。この加工工程は、上述してきた焼成工程の後工程になり、最終製品として仕上げる工程である。
といっても数十ある製品群ごとに在庫を管理しようとすれば、見える化の作業だけで大きな手間が掛かる。そこで製造法別に8つに分類したうえで、IT(情報技術)で種別ごとの仕掛かり在庫量を管理した。この見える化によって、日本特殊陶業社内の焼成工程から送り出す仕掛かり品の量を、社外の工場の仕掛かり量に応じて調整できるようになった。
社外の取り組みの2つ目は、投入順を順守してもらい、勝手に投入順を変えたり、仕掛かり在庫をためたりさせないことだった。そこでDBRの考え方について勉強会を開催し、浸透を図った。
DBRに基づく投入スケジュールの管理が2006年後半からはグループ会社以外の加工の外注先にも広がり製造量の70%をカバーした。8週間かかっていた通常納品(別注品の追加注文)の注文から納品までの期間は4週間に半減し、製造工程全体の仕掛かり在庫も半減した。
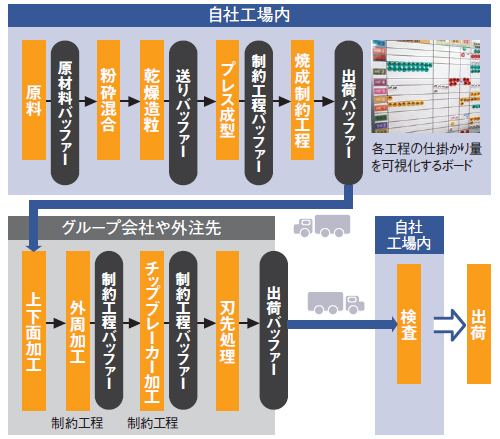