掘り下げ力の意義は、根本の原因や顧客の要望を的確に理解できるようになるだけではない。課題を掘り下げながら考え、問題の全体像や解決策を整理して伝えるスキルを従業員が身につけると、改革や改善への意識がそろいやすくなる。
組織的に掘り下げ活動に取り組んで改革のスピードを高めている成功事例が、切削工具の大手メーカー、日立ツールの滋賀・野洲工場だ。
精鋭部隊が全体像を把握して方針作成
2006年のある日、野洲工場は「7デイズ・プロダクション」という指令を本社から受け取った。生産リードタイムが最短で14日だった切削工具の「超硬エンドミル」を、7日以内で生産できるように工夫せよという指令だった。
野洲工場は2000年に、イスラエルの物理学者であるエリヤフ・ゴールドラット氏が考案したTOC(制約条件の理論)の手法を全面的に導入。TOCの生産改革手法であるDBR(ドラム・バッファー・ロープ)などを駆使して効率化を進めてきた。超硬エンドミルの生産リードタイムは、2000年時点で約2カ月かかっていたのが、2006年には14日間に短縮した。棚卸資産の手持日数は30日程度。競合他社の平均の半分以下に縮めた。
これだけリードタイムを縮めてきたにもかかわらず、さらに半分にするように本社は求めてきたわけだ。工場全体で一丸となって協力して解決できるかどうかという相当な難題である。
野田修工場長は高度な要求に苦笑いした。しかしすぐに奮い立ち、腹心の新見章彦製造センター長兼生産技術センター主任技師ら「TOC推進事務局」のメンバーに対策の検討を指示した。
TOC推進事務局は、役職無しの若手からベテランまで約40人で構成する部門横断型の精鋭組織だ(写真1)。「精鋭が主体となって横断的に話し合って問題を掘り下げ、解決策を打ち出し、TOC活動に対する若手の理解を促進するなどの役割を担っている」(野田工場長)
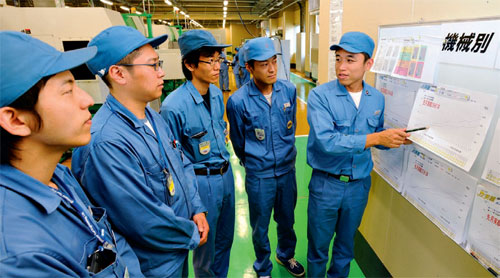
早速、1カ月に2日間開いているワークショップで生産リードタイム短縮のための掘り下げ活動に入った。
目標までの道のりを“地図”で整理
問題の掘り下げには、TOCの手法の1つである「思考プロセス」を駆使する。思考プロセスは、なぜなぜ5回のように問題を1つずつ順番に分析する手法とは異なったやり方で解決策を掘り下げる。問題点をいったんすべて洗い出して、それぞれの関連性を整理しながら、手順や方針が対立する要素を見つけ出し、それらを解決できる発想や手順を探るのが特徴だ。
TOC流の生産改革は、「部分最適と全体最適の対立」という視点で問題を整理しつつ、「ボトルネック工程を特定すれば解決できる」という視点で突破口を見いだすことが一般的だ。例えば、「各工程が仕掛かり在庫を作りだめする」行為と「ライン全体で在庫を減らす」行為が対立しているとしよう。現場が仕掛かり在庫を作りだめする理由が「工程別の稼働率を高める方針がある」ことだとすれば、「部分最適を助長する工程別の稼働率管理をやめ、ボトルネック工程に合わせたペースでほかの工程が生産する仕組み」が解決策になる。