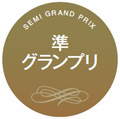
セイコーエプソンは2008 年11月、グローバルSCM(サプライチェーン管理)システムを稼働させた。インクカートリッジなど約6000品目のプリンタ用消耗品のデータを管理する。日本、北米、欧州、アジアにある計20拠点の生産・販売・在庫データを一元管理することで、半年で70 億円分の在庫を削減した。複雑な商品・資材の管理コードをグローバルで統一したことが大きな成功要因だ。今年5月には、新型インフルエンザ対応でも効果を発揮した。
セイコーエプソンは2008年11月、日本、北米、欧州、アジアにある計20拠点を結ぶグローバルSCM(サプライチェーン管理)システムを稼働させた。インクカートリッジなど約6000品目のプリンタ用消耗品の生産・販売・在庫データを一元管理する。
同社はシステム稼働に合わせて、生産・出荷計画にかかわる業務プロセスを大きく変えた。拠点ごとに計画を立案していた体制をやめ、中核事業所である広丘事業所(長野県塩尻市)で世界20拠点の生産・出荷計画を立案したり実績を管理したりする体制を築いた(図1)。さらに、計画立案のタイミングを月次から週次に短縮することで、需要変動に素早く対応できるようにした。
成果はすぐに表れた。システムを稼働させてからわずか半年で、約70億円分の在庫を削減できたのだ。生産・出荷計画にかかわる業務工数も約30%削減した。「景気変動や消費動向の変化が激しい今、勘と経験だけでは在庫をコントロールできない。(データを基に判断する)あるべき姿に、やっと近づいた」。セイコーエプソンの井口信夫機器事業企画・管理部長は語る。
インクカートリッジなどの消耗品ビジネスは、プリンタ事業において重要な収益源である。販売機会を逃さないためには、在庫切れは避けなければならない。そのため家庭用プリンタ市場が急速に拡大していた1990年代後半から2005年ころまでは、「とにかく市場に商品を供給する」ことが至上命題だった。
しかし、事業が世界規模で拡大し、品目数が急増すると課題が出てきた。「在庫」である。供給優先で完成品や原材料、資材の在庫が増えた結果、それらが企業収益を圧迫し始めたのだ。「商品を安定供給しつつ在庫を増やさないためには、システムを活用して正確かつ俊敏に在庫をコントロールすることが不可欠だった」(井口部長)。
在庫を最適化するにはどうするか--。セイコーエプソンはグローバルSCMプロジェクトを進めるに当たり、三つの目標を掲げた(図2)。「データの可視化と共用化の推進」「生産・出荷計画立案の集中化(ワンヘッド化)」「計画サイクルの短縮」である。
商品や資材の管理コードを世界で統一
グローバルSCMプロジェクトの三つの目標を達成するために、避けて通れないのが商品や資材を管理するコードの統一だ。プロジェクトが始まる前から、生産や物流を管理するシステムは拠点ごとに構築してあったが、「データの管理コードがバラバラ。データを集約しても、それぞれが何を意味しているのかわからない状態だった」(機器情報化推進部の澤田隆治主幹)。
この課題を解決するために、各拠点のデータを変換して読み換える方法がある。しかし、澤田主幹は「場当たり的な対策は意味がない」と考え採用しなかった。6000品目、部品点数に換算すると数万種類を超えるデータの変換テーブルをメンテナンスし続けることは難しい。品目が変わると変換テーブルを作り直さなければならないし、システム側で把握していない管理コードを拠点が勝手に割り当てたらコードを正しく変換できなくなる。
約10年前から各拠点の管理コードを統一する作業に取り組んでいたが、進んでいなかった。グローバルSCMプロジェクトが立ち上がったのを機に、経営層のトップダウンで一気にコード体系を統一した(図3)。
さらに、コードで管理する情報の粒度も細かくし、工場内や物流センターの「どこに、何があるか」まで把握できるようにした。例えば、インクカートリッジの部品が「工場Aの倉庫にある」「工場Bの生産ラインαにある」「生産ラインβのオンボード(生産工程)にある」「物流センターCの入庫倉庫にある」といった情報は、管理コードの意味をシステムで解釈すれば即座にわかる。
「おおざっぱなデータでは、どんなにデータを収集・分析しても“甘い”計画になる。資材や商品のロケーションを細かく把握することで、実態に基づいた生産・出荷計画を立てられる」と澤田主幹は指摘する。